Replica molding (REM) - Adam Selsman
Replica molding (REM)
Replica molding (REM) is a form of soft lithography which utilizes materials such as polydimethyl-siloxane to create microfluidic devices through duplication of shape and structure of a mold. REM typically is used to mold patterns with features on a nano-scale that often are too difficult for other forms of molding (i.e. injection molding) to replicate. A wide range of products ranging anywhere from CD's to various biomedical devices are created using Replica molding.
PDMS

Poly(dimethyl-siloxane) is a silicon based organic polymer that has very unique flow properties and is the most common compound used in soft lithography. Since PDMS is a stiff elastomer (Young's modulus of ~0.5 MPa) and has the ability to be high in fidelity, it makes it the perfect compound to mold to a structure because it conforms to the nano-scale details of a microfluidic device on an atomic-level. PDMS is normally hydrophobic but can become hydrophilic when oxidized, allowing it to bind and separate to many different types of molds and substrates. On top of it's binding ability, the actual compound is both transparent and non-toxic giving it two major benefits for microfluidic devices. The first advantage is that due to PDMS's non-toxic nature, it allows for culturing of cells directly on a device as well as potential in vivo implantations. The second benefit is due to PDMS's transparent nature, allowing a number of detection schemes to be used on the mold, such as UV absorbance or fluorescence. On an industrial level, PDMS is both very cheap to produce and purchase.
Physical Process

Replica molding (REM) takes place once a master for the device is created from rapid prototyping. REM is used as the primary method of channel creation in the molding compound. Replica molding creates a negative-photoresist replica of the original design onto the prepolymer, usually PDMS. Once the prepolymer is set onto the master, the prepolymer is either heat treated using an oven or UV treated under a UV lamp, depending on the type of mold and master compounds. Before treatment has begun, sterilized posts are put in to create various ports and entry channels to be molded into for the resulting replica.
This process creates three sides of the device and the final side is created using either reversible or irreversible sealing. Reversible sealing is the most common and is attached by adding another layer of PDMS over the area for the fourth wall, which seals on its own due to the intrinsic van der Waals contact in PDMS. The fourth wall can be removed and then resealed due to the weak van der Waals forces being unable to withstand higher pressure, allowing it to be used multiple times. Irreversible sealing which is less common involves substrate binding between the replica mold and the fourth wall through facilitation by exposure to some form of air plasma.
The compound sealed is typically another piece of PDMS or glass. Once water is removed from the system, silicon-oxygen bonds are created (Si-O-Si) forming tight seals. Using glass will create an irreversible seal that, when attempted to be broken, shatters the PDMS replica mold. While more PDMS and glass are the most common final walls, other compounds such as quartz, polyethylene, and polystyrene can also be used and sealed to the mold.
Advantages of REM
There are a few major advantages to creating molds through Replica molding. The biggest advantage is that you can create 50+ from the creation of one mold from the master. This drastically decreases both spending and time to create specific patterns that would consistently be used in creating various devices. Another major advantage is that REM works with a wide variety of compounds and polymers so that the device can be created specific to the desired compound. The final advantage is that REM can create molds that cover a wide range of surfaces including non-planar curved shapes, and large area masters. Replica molding is a very useful universal pattern replicating technique that can be used for a wide variety of shapes and compounds, without many issues.
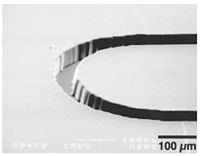
References
[1] McDonald, J. C.; Anderson, J. R.; Duffy, D. C.; Chiu, D. T.; Wu, H.; Whitesides, G. M. Fabrication of microfluidic systems in Poly(Dimethylsiloxane). Electrophoresis 2000, 27–40. [2] Qin, D.; Xia, Y.; Whitesides, G. M. Soft lithography for micro- and nanoscale patterning. Nature Protocols 2010, 5 (3), 491–502. [3]Xia, Y.; Whitesides, G. M. Soft Lithography. Annual Review of Material Sciences 2010, 29 (25), 153–184. [4] Xia, Y.; Mcclelland, J. J.; Gupta, R.; Qin, D.; Zhao, X.-M.; Sohn, L. L.; Celotta, R. J.; Whitesides, G. M. Replica molding using polymeric materials: A practical step toward nanomanufacturing. Advanced Materials 1997, 9 (2), 147–149. [5]Mata, A.; Fleischman, A. J.; Roy, S. Characterization of Polydimethylsiloxane (PDMS) Properties for Biomedical Micro/Nanosystems. Biomedical Microdevices 2005, 7 (4), 281–293.